A question we are frequently asked by maintenance engineers is how often specific types of hoses should be replaced. Leaving it too late to replace a hose in need of attention greatly increases the risk of a failure, likely causing safety issues and unplanned downtime.
We often recommend a maintenance plan specifically for hoses to supplement standard preventative servicing by providing information on individual hoses. By tracking the lifecycle of each individual hose, including frequent inspections and pro-active replacements, failures can be kept to a minimum. Whilst developing a separate plan may seem challenging, the cost-saving benefits make it worth the initial investment of time and planning.
The lifecycle of each hose varies due to its application and the medium flowing through it, therefore requiring a unique replacement interval based upon its environment. Everything from pressure to viscosity of the fluids carried should be taken into consideration.
Imagine an application that uses 40 identical hoses. 20 of these hoses are located in a high temperature environment and wear out after 12 months, whilst the other half operate at ambient temperature and last twice as long. Replacing all hoses on a 2-year maintenance cycle is dangerous and can potentially lead to unexpected failures. An experienced maintenance crew will understand the cost to operations of unscheduled downtime and will replace hoses pro-actively to avoid unscheduled shut downs.
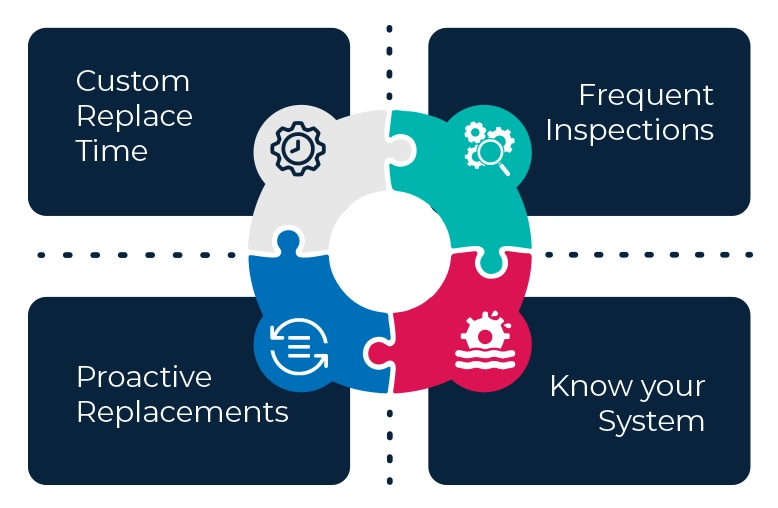
Creating a hose maintenance plan
Whilst we can supply you with general inspection and replacement guidelines, your real-world intervals will vary based on each hose’s operating environment, materials of construction, and several other factors. As such, your replacement intervals should be determined through observation and meticulous record-keeping.
Step 1. Identify your hoses
The first step should always be a full audit that identifies and tags each individual hose. This can often be completed for free by your supplier – Click HERE to request your FREE hose audit. The process will tag each hose with a serial number, noting the hose type, part number, process fluid, pressure and temperature ratings.
The added benefit is that when re-ordering a hose, you simply need to quote the serial number, as your supplier will already hold a record o the hoses length, end connectors and material, along with the date of install and schedule of replacement.
Step 2. Track each hoses lifecycle
Perform regular hose inspections, examining each hose at an interval recommended by your supplier. Visual inspections do not require downtime and allow you to check for signs of wear, splits, corrosion, bends, and overall deterioration. Once a hose has reached its end of life, it is imperative to note its service interval to inform your replacement period for that type of hose. If a hose breaks unexpectedly, document all aspects of the failure, and alter the service interval as necessary.
Step 3. Eliminate unnecessary wear and tear
Check for conditions putting strain on your hoses during operation. Inspect for rubbing against other hoses or another source of friction, or exposure to heat sources. Findings should be corrected immediately, lest they shorten the lifecycle of your hose, potentially causing failure.
Step 4. Identify if protection is needed
Hoses sometimes require additional protection to withstand the environment in which they operate; For instance, shielding from weld splatter or resistance to UV light, insulation from high-temperature external machinery, or guards against bending and abrasion. Whilst these hose covers in no way change the make-up of the hose itself, it is important to understand the conditions of operation.
Step 5: Analyse your historical maintenance
Periodically check your hose inspection log against frequency of replacement to determine if any intervals should be shortened. In addition, if a specific hose is replaced often, consider using an alternative design that will offer a longer lifecycle. Any supplier who manufactures their hoses in-house will be able to help design a comprehensive replacement.
Having a hose maintenance plan can lead to significant cost savings, less downtime, and improved workplace safety. With a plan in place, your engineers can order replacement hoses simply and easily, whilst sticking to a regular maintenance schedule that should eliminate the majority of failures. Once you start to track these number, you will immediately see the value of your investment.
To speak to us about a free hose audit, or to get help setting up your own hose maintenance plan, drop us an email on industrial@mpcc.co.uk or call 0113 289 0 281